1.3Technical data of generator Manufacturer | FARADAY (CHINA) | Type | FD6E-4 | Rated power | kW | 1,000 | Rated current | A | 1,800 | Frequency | Hz | 50 | Voltage | V | 400 | Speed | rpm | 1,500 | Permissible over speed | rpm | 1,875 | Power factor | 0,8 | Efficiency at rated load | % | 94.40% | Construction | Single bearing | mode of connection |
| Voltage regulator | DVR2000 | Voltage regulating mode | AVR automation | Excitation method | Brushless | Cooling way | Air cooling naturally | Cooling air volume | CFM | 2875 | Heat rejection rate | Btu's/min | 3472 | Full load torque | Lb-ft | 5119 | Winding pitch | 2/3 | Protection Class | IP 23 | Insulation class | H | Maximum ambient temperature | °C | 40 |
2 Technical parameters
2.1 Natural gas consumption Genset selection is suitable for pipeline natural gas (dry gas). According to standard environment condition (Barometric pressure 1000 mbar or 500m above sea level, air temperature 25�? relative humidity 30%), All data in the technical specification is based on engine full load at specified temperature and the methane number and subject to technical development and modifications.
2.2 Gas purification requirement (at module) other constituents | oil and water | dust particle size | Hydrogen sulfide | content | No liquid composition | < 10mg/m3 <5μm | <20ppm |
Natural gas temperature: 5 - 45°C; Natural gas pressure: 100kpa - 400kpa(Pressure governor before ) or 8kpa - 15kpa(without pressure governor)
2.3 Environment condition Under the environment: air temperature is in -20℃~+40�? relative humidity below 90% (20�?; Altitude below 1000m, genset is able to run steadily and reliably. 2.4 Technical norms Genset in accordance with the relevant IEC standards GB2820-1997, JB/T9583.1-1999 and IEC439. The production process carry out the related quality system ISO9001. 2.5 Engine gas piping process Gas engine natural gas intake system configure manual ball valve, filter, pressure governor (optional), solenoid valve, natural gas control valve, these are monuted on the genset. 2.6 Coolant system (at module) Radiator is mounted on the genset. Coolant water is demineralized water; hardness is between 0.7�?.3mmol/L; the content of chloridion is less than 150mg/L; PH value�?�?.5. Regularly check the water tank liquid level height and timely supplement. 2.7 Control system and electrical equipment The Max. environment temperature is less than 40°C. On this condition, relative humidity less than 70%. Altitude below 1000. 2.8 Room specifications ●room structure should achieve a level fire rating. ●In accordance with the explosion-proof requirements, it should deploy a forced ventilation system indoor. Other appliances in the genset room will be adopted explosion proof equipment, put an end to an ignition source. ●Gas leakage protection: two unit combustible gas alarm probe, one unit combustible gas alarm. ●Separated from the operating room and the room�?/p> ●fire-fighting equipment. ●lightning conductor. ●Genset installation: The ground should be compacted to pour concrete foundation; The genset is arranged on the horizontal ground; and it is fixed installation. ●Room should be set up corresponding cable trench, drainage ditch; and the rational layout of natural gas pipeline.
3 Scope of supply - module Design: The module is built as a compact package. Engine and generator are connected through a coupling and are mounted to the base frame. vibrations are eliminated by mounting the module on isolating pads. 3.1 Spark ignited gas engine Four-stroke, air/gas mixture turbocharged, aftercooled, with high performance ignition system and electronically controlled air/gas mixture system. The engine is equipped with the most advanced
LEAN-BURN COMBUSTION SYSTEM
3.1.1 Engine design Engine block Single-piece crankcase and cylinder block made of special casting; crank case covers for engine inspection, welded steel oil pan. Crankshaft and main bearings Drop-forged, precision ground, surface hardened, statically and dynamically balanced. main bearings(upper bearing shell: grooved bearing/lower bearing shell; sputter bearing) arranged between crank pins, drilled oil passages for forced-feed lubrication of connecting rods. Flywheel With ring gear for starter motor and additionally screwed on. Pistons Single-piece made of steel, with piston ring carrier and oil passages for cooling; piston rings made of high quality material, combustion chamber specially designed for lean burn operation. Cylinder head Specially designed and developed for burn engines with optimized fuel consumption and emissions; water cooled, made of special casting, exhaust and inlet valves made of highquality material. Combustion air / fuel gas system Automatic control valve for automatic adjustment according to fuel gas characteristic. water-cooled or air to air intercooler, throttle valve and distribution manifolds to cylinders. Ignition system advanced, fully electronic high performance ignition system, external ignition control. Lubricating system Gear-type lube oil pump to supply all moving parts with filtered lube oil, pressure control valve, pressure relief valve and full-flow filter cartridges. Cooling of the lube oil is arranged by a heat exchanger. Engine cooling system Jacket water pump complete with distribution pipework and manifolds. Gas train Pre-assembled, delivered loose, for installation into gas pipework to the module. Consisting of�?/p> ●Gas filter cartridge unit Fine cartridge filter in welded configuration, built on supports. Dust protection grade: > 2μm 92%, 99% >5μm Attention:the filter installed in the gas train is only a safety filter. The particle content in the fuel gas can lead to a quick pressure rise over the safety filter. correspondingly sized filters should be installed on site (not scope of supply) if required. ●Main gas train: Manual ball valve Solenoid valves Pressure gauge Flame arrestor ( Option ) Gas pressure regulator The gas train must be fitted with a heating system in order to avoid condensate formation -> customer scope of supply. Maximum distance from main gas train outlet to gas entry on engine, including flexible connections, is less than 2 m. -> customer scope of supply. BUYER must provide: real-time gas analysis. Exhaust system Turbocharger and exhaust manifold Electric actuator For electronic speed and output control Starter motor Engine mounted electric starter motor
3.1.2 Standard tools The tools required for carrying out the most important maintenance work are included in the scope of supply and delivered in a toolbox. 3.2 Generator - 400V Magna PLUS generators are a brushless, self excited, externally voltage regulated, synchronous AC generator. The generator is made up of six major components: main stator (armature), main rotor (field), exciter stator (field), exciter rotor (armature), rectifier assembly, and voltage regulator. stators are stationary, rotors rotate, a field is an electrical input,and an armature is an electrical output. Electrical Performance: Class H insulation. Standard 12-wire re-connectable winding, 2/3 pitch, type no. 6 High efficiency and motor starting capacity. Total harmonic content < 50; TIF �?% Electrical data and features: • Standards: IEC 60034, EN 60034, VDE 0530, ISO 8528-3, ISO 8528-9 | •Transient voltage regulation rate: | +20/- 15% | •Voltage adjustment range�?/span> | -/+ 5% | •Overload capacity: | 110% | •No-load line voltage waveform sine distortion rate: | < 5% | •Altitude: | <1000m | • Max permitted generator intake air temperature: | 5°C - 40°C | • Max. relative air humidity: | 90% |
3.3 Engine generator control panel - AGC150 The AGC 150 Engine Drive is designed for OEMs and system designers who require simple, flexible, and reliable engine control for various applications. It comes with a built-in application that protects the engine from overload and supports various start and stop sequences, from simple start and stop to pump functions with manual RPM control or regulation via flow or pressure control. The controller supports Stage V emission requirements. The AGC 150 Engine Drive offers a wide selection of configurable inputs and outputs, including CANbus ports for connecting an additional operator panel and an Ethernet port for Modbus communication or for configuring the unit using DEIF’s free PC tool utility software. The IP65 certified front-mounted controller is easy to mount, and easy to use thanks to its graphical display unit available in 11 languages. 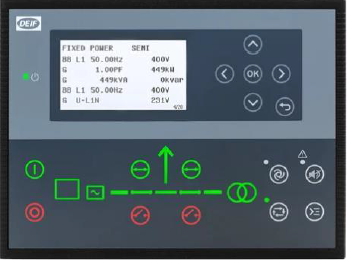
3.4 Starting system Starter battery: 2 piece 12 V battery. Battery voltage monitoring: Monitoring by an under voltage relay. 3.5 Flexible connections Following flexible connections per module are included in scope of supply: No. Connection | Unit | Dimension | Material | 1 Exhaust gas outlet | DN | N.A | Stainless steel |
Sealings and flanges for all flexible connections are included.
3.5.1 Flexible connections Totally enclosed floor mounted sheet steel cubicle with front door wired to terminals. Ready to operate, with cable entry at bottom. Naturally ventilated. Protection�?/span> | IP 42 external | IP 20 internal |
Ambient temperature: 5 - 40 °C (41 - 104 °F), 70 % Relative humidity.
3.5.2.Supply list
No | Item | Description | Specification | Qty | Remark | 1 | Natural gas generator set | Natural gas engine | K50N-G10 | 3 | Including engine, air filter, ignition, speed control system and connecting pipe lines, cooling water tank, etc. | Alternator | FD6E-4 | 3 |
| Base |
| 3 | With shock pad | Muffler and bellows 消声器及波纹�?/span> |
| 3 |
| Documentation, tool kits, etc. 文件资料、工具包�?/span> |
| 3 |
|
| Gas pre-valve group | Explosion-proof Gas cut-off solenoid valve | DN100 working pressure within 2bar | 3 | EX | Pressure regulating valve | DN100 working pressure within 2bar | 3 | MADAS | 2 | Filter | DN100 working pressure within 2bar | 3 | MADAS | Flame arrestor | DN100 working pressure within 2bar | 3 | EX | Connecting pipe | DN100-7 | 3 |
| Pressure gauge | ±20KPA | 3 |
| Manual shut-off valve | DN100 | 3 |
| 3 | Controller | Parallel Control cabinet | Deif AGC 150 CHINT Frame Circuit Breaker | 3 |
|
4 Delivery, installation and commissioning
4.1 Carriage to shanghai port. 4.2 Unloading:by buyer 4.3 sea transport:by buyer 4.4 Assembly and installation By buyer.(seller supply installation file)
5 Limits of delivery Electrical Module: At terminals of module interface panel At terminals of generator terminal box Exhaust gas At outlet flange of exhaust gas connection Combustion air The air filters are set mounted Fuel gas At inlet and outlet flanges of gas train Attention�?/p> The first filling of module�?lube oil, engine jacket water,anti freeze-, anti corrosive agent) is not included in our scope of supply. The composition and quality of the used consumables are to be strictly monitored in accordance with the "Technical Instructions" of Omnitek. Suitable bellows and flexible connections must be provided locally for all connections. Cables from the module must be flexible.
Insulation Insulation and pipework is not included in our scope of supply and must be provided locally.
5.1 Factory tests and inspections The individual module components shall undergo the following tests and inspections: 5.1.1 Engine tests The following tests are made at 100%, 75% and 50% load, and the results are reported in a test certificate: • Engine output | •Jacket water temperatures | • Lube oil temperature | •Exhaust gas | • Fuel consumption | • Lube oil pressure | • Boost pressure | temperatures |
5.1.2 Generator tests Carried out on test bench of the generator supplier. 5.1.3 Module tests The engine will be tested with natural gas (methane number more than 95). The following tests are made and the results are reported in a test certificate: ●Functional tests per technical specification of control system. ●Starting in manual and automatic mode of operation ●Power control in manual and automatic mode of operation ●Function of all safety systems on module ●Measurements at 100%, 75% and 50% load ●Frequency ●Voltage ●Current ●Generator output ●Power factor ●Fuel consumption ●Lube oil pressure ●Jacket water temperature ●Boost pressure
|