100MW Photovoltaic Module Project Plant Area Planning Factory Building Construction Scale The factory building of this project (photovoltaic module factory) will include production workshops, warehouses, office and living areas, and supporting facilities to meet the technological requirements of photovoltaic module production and the work needs of employees. The expected floor area is not less than 16,600 square meters, of which the building area is not less than 13,600 square meters. The main construction content and scale are as follows: Engineering Category | Section Name | Expected Number of Floors | Floor Area (m�?/span> | Building Area (m2) | Building Type | Main Production System | Production Workshop | 1 | 2500 | 2500 | Light Steel / Brick - Concrete |
| Auxiliary Workshop | 1 | 1000 | 1000 | Light Steel / Brick - Concrete |
| Finished Product Warehouse | 1 | 1200 | 1200 | Light Steel / Brick - Concrete |
| Raw Material Warehouse | 1 | 800 | 800 | Light Steel / Brick - Concrete | Auxiliary Production System | Comprehensive Office Building | 2 | 1000 | 1000 | Brick - Concrete |
| Staff Dormitory and Canteen | 2 | 600 | 1200 | Brick - Concrete | Total | 7700 |
| Supporting Facilities | Peripheral Equipment | 1 | 300 | 300 | Brick - Concrete |
| Living Facilities and Parking Lot | 1 | 800 | 800 | Light Steel |
| Road Construction | 1 | 1000 | 1000 |
|
| Greening and Others | 1 | 500 | 500 |
| Total | 2600 |
|
The factory building area is approximately 16,600 m2, including component production workshops, finished product warehouses, raw material warehouses, comprehensive office buildings, staff living areas, and power plant public auxiliary projects. A new production line for high - efficiency solar photovoltaic modules and BIPV structural parts will be built, and the roof of the factory building for high - efficiency solar modules used in green building integration will be installed and constructed. Factory Building Structure Form The project construction is designed in full accordance with the requirements of modern enterprise construction, using light steel, frame structure, and brick - concrete structure. The entire factory building is equipped with skylights for lighting and natural ventilation. The building of the production workshop has good overall structural performance, convenient construction, and cost savings under the premise of complying with the current relevant local codes. The principle of general layout is to have a reasonable layout, save land, and reserve appropriate development space. The factory buildings are arranged in a smooth flow with light steel and brick - concrete structures, and the roads, water, electricity, and gas pipelines are connected smoothly. 2. According to the overall factory area planning, the factory fence adopts an iron fence. The whole factory is designed with two entrances and exits, and the factory roads are circular, divided into main and secondary roads, connecting each entrance and exit to form a smooth transportation and fire protection channel. The steel structure is installed and welded according to the design plan, and the wall materials are heat - insulating and waterproof to ensure the waterproof and thermal insulation effect of the exterior wall. The roof has good light transmittance to utilize natural light. 3. Building Requirements: n Overall flatness of the factory building: ±10mm n Factory building height: at least 6 meters, and the height of the maintenance space is related to the factory building height n Load - bearing: at least 1.3T / m2 (except for the laminator area) 4. Construction requirements for the production workshop: n Unless otherwise required, the illumination, temperature, humidity, atmospheric pressure, and ventilation and exhaust facilities in the workshop should meet the requirements of general electronic product assembly workshops. n The welding, component lamination, and laminating work areas should be general purification workshops, and the room temperature should be 25°C - 30°C. n The room temperature at the component testing station is 25C - ±5C. Based on the above requirements and the needs of each process, the workshops to be built include raw material warehouses, component production and packaging lines (clean workshops), component maintenance lines (clean workshops), raw materials, and finished product warehouses. Supporting Facilities of the Factory Building To ensure the normal operation of the component production workshop, we recommend the following supporting facilities: 1. Power supply system: According to the power and lighting needs of the production workshop and living and office areas, it is recommended to equip a stable power supply system and consider the installation of grid - connected power generation and energy storage equipment to meet the demand for photovoltaic power generation. 2. Water supply system: It is recommended to configure a stable and reliable water supply system, including tap water supply and circulating water supply, to meet the production and living needs of employees. 3. Drainage system: It is recommended to configure a drainage system, including sewage treatment facilities and rainwater collection systems, to treat and discharge the production wastewater. 4. Air - conditioning and ventilation system: It is recommended to configure a high - efficiency and energy - saving air - conditioning and ventilation system to provide a comfortable indoor environment and good working conditions. 5. Gas supply system: (Air compressor station, protective gas supply situation) Air pressure requirement: 0.6 - 0.8 MPa The production line can be equipped with 2 air compressors of 75KW or 1 air compressor of 100KW. 6. Fire protection system: It is recommended to configure a complete fire protection system, including fire alarms, fire hydrants, and fire - extinguishing equipment, to ensure the safety of the factory. 7. Monitoring system: The whole factory building, office building, workshop, staff living area are monitored, and the network system is supported. The factory area lighting adopts solar - integrated street lights. 8. The entire power consumption of the factory building is based on the equipment drawing line layout, the selection of cable trays, and the routing of gas pipeline dredging; the wiring of electrical lines entering the workshop is through cable trays, and the connection direction of the compressed air source and equipment will be communicated with the equipment manufacturer after the equipment is confirmed and purchased.
Outside the Factory Building The design of water supply and drainage should comply with local policies and design specifications according to the planning and design requirements. 4.1 Water supply design: • A: Water source: Supplied by the local tap water pipe network, and the introduced pipe diameter is not less than DN150. • B: Indoor water supply: The domestic water supply is provided by the local tap water pipe network, and the water quality meets the domestic drinking water standard. • C: Fire water supply: The fire water supply pipe adopts a hot - dipped galvanized steel pipe, and the fire protection facilities are configured in accordance with local requirements. The distance between fire hydrants is not greater than 30 meters to ensure that two streams of water can reach the fire extinguishing point at any part of the same floor at the same time. • D: Outdoor ground fire hydrants are set, and the water supply network system is arranged in a ring shape to ensure that a fire extinguishing point can be formed at any part of the building. 4.2 Power supply: n Incoming main power supply: Three - phase 380V 50Hz three - phase 5 - wire, single �?/span> phase 220V The maximum peak value of the production line equipment is: [2035KW]. Therefore, a transformer with a total capacity of 2500 - 3150kVA can be selected, and the combinations that can also be selected are: 1250kVA + 1250kVA, 1000kVA + 1600kVA, 800kVA + 1600kVA, 630kVA + 2000kVA, 500kVA + 2000kVA, etc. 4.3 Road design: n The layout principle of the factory roads should meet the requirements of enterprise transportation, fire protection, pipeline layout, and greening, and meet the requirements of convenient and smooth traffic. According to the plane layout in the factory area, a circular road is set, which is a concrete pavement with a width of 6 meters for the main road. This main road is mainly used for transporting raw materials and finished products out of the factory. The road design should not only meet the business structure process but also meet the fire protection requirements.
4.4 Staff living area: The factory area is equipped with supporting facilities such as dormitories and restaurants in the living area. Secondly, the produced photovoltaic modules are installed on the roof for demonstration application projects, and the electricity generated by photovoltaic air energy is used for heating to save energy and reduce emissions.
Equipment Configuration List Refer No: BPF407202403060098-10277 other 20 Semi-automatic equipment, approximately 80 people are required, with a two-shift system. 100MW Component Production Equipment Configuration List |
| Serial Number | Name | Quantity | Unit | Remarks | 1 | Slicer | 1 | set | High - speed non - destructive | 2 | Stringer | 1 | set | Autowell 050E | 3 | Lamination Welder | 1 | set |
| 4 | Laminator | 1 | set | Single - layer double - cavity 2787 | 5 | Layout Machine | 1 | set |
| 6 | Cutting Machine | 2 | set |
| 7 | EL Integrated Machine | 3 | set |
| 8 | Manual Edge - trimming Table | 1 | set |
| 9 | Appearance Flipping Inspection | 1 | set |
| 10 | Frame Gluing Machine | 1 | set |
| 11 | Framing Machine | 1 | set |
| 12 | A - B Glue Filling Machine | 1 | set |
| 13 | Curing Line | 1 | set | Manipulator automatic loading and unloading | 14 | 180 - Degree Flipping Table | 2 | set |
| 15 | IV Tester | 1 | set |
| 16 | Stacker | 2 | set |
| 17 | Assembly Line | 1 | set |
| Equipment Cost Total |
| Peripheral Equipment | Air Compressor | 1 | set |
| Dryer | 1 | set |
| Cooling System | 1 | set |
| Power System | 1 | set | Secondary distribution 650KW | Other | Building Cost | 8800 | m | Excluding road construction, greening and others. | Equipment Installation and Commissioning Cost |
| Technical Service On - site Guidance Fee | Annual fee (converted) | Equipment Transportation Cost |
| Foreign Customs Clearance Cost | Customer is responsible, not included |
|
|
|
|
|
|
Factory Building Layout Plan 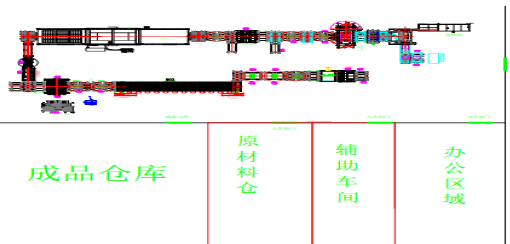
|