Company Profile Supplier is a modern entity enterprise that includes research and development, production, sales, after-sales departments. We already developed and produced the suitable equipments for the organic fertilizer and bio organic fertilizer production, such as the compost equipment, drying equipment, granulating equipment, screening systems and batching systems, and a full set of fertilizer equipment. Our company has strong technical strength, high-quality staff and CAD design center, for enterprises to provide fertilizer plant design, process improvement, equipment manufacture, installation, commissioning, formula and a series of comprehensive services, products cover all over the country. The company's main products: ground walking pile turning machine, groove turning machine, crusher, mixer, granulating machine, drying machine, cooling machine, screening machine, packing machine, dustdesulfurization equipment, according to the customers' requirements, to design the 10 thousand -50 million tons complete sets of organic fertilizer production line and workshop design, and to supply complete sets of organic fertilizer and inorganic fertilizer equipment, bulk blending equipment, high and low tower fertilizer equipment , drum steam mixture fertilizer equipment, urea formaldehyde fertilizer equipment, ammonia acid fertilizer equipment, ammonia fertilizer equipment, melting equipment, spraying fertilizer of urea based ferilizer spraying equipment, extrusion equipment and other high manure fertilizer wet material drying equipment for fermentation. For organic and inorganic fertilizer plant, garbage, sewage treatment plant, opened up a precedent for treatment of organic waste harmless. Self - developed multifunctional compound fertilizer complete set of equipment has the characteristics of compact space and minimum operating dust entrainment Enterprise Aim: Adhere to the market-oriented,innovation for development,quality for survival,to improve after-sales service to win the trust of customers. Warmly welcome friends from all industries to guide and negotiate business! Voltage: 380V, 3 phase, 50HZ(Accept custom Capacity:8-10 T/ H Abby31202411270132-98402 Item | Power | Quantity | Ferment turner machine | / | 1Set | Crush-Screening | 75.5 KW | 8 Sets | Granulator Production line | 315.97kw | 33sets |
|
|
| FOB costs (need 10sets 40ft high containers for the whole line) | Total | 337.12KW | 42 Sets |
Trade Terms: Trade type:FOB Qingdao China Machine warranty:1 year(don’t contain Wearing parts) Note: Dryer machine, Cooler machine will connect with Hot stove, Dust Collector room with pipes, pipes length will be calculated and add in quotation after designed the drawing. Seller will supply the cable layout
Organic fertilizer granulating plant include 3 areas: 1), Raw material fermentation area: Necessary composting and fermentation process will Kill harmful microorganisms and eggs.According to different material and climate, compost time is with 10-25 days. 2), Raw material preparation area:Raw Material Preparation Area Production Flow: The material before granulating should be fine powder, without impurity, such as wood branch, stone, glasses, fabric..................... …and so on. So, please use the loader take the material after finish fermentation into the feeding hopper, after crushing,screening, and get the fine powder shape raw material, like follow flows: 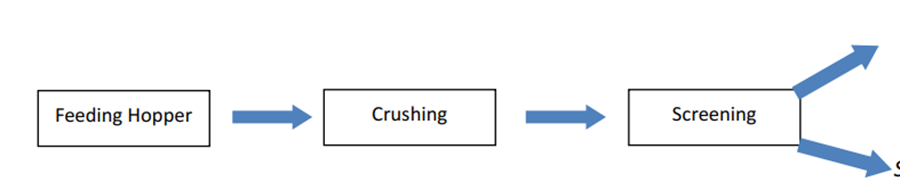 | Separating the impurity material. | Separating the fine compost fine powder material for granulating |
If your raw material is all already powder and ready to granulate, the above parts can reduce as the situation 3), Organic fertilizer Granulating Area: Organic fertilizer granulating area production flow: The granulating technology belong to wet granulating technology. You will add other additive material to promote the quality of organic fertilizer finally.So, we have to consider the formula, and use the batching system in the beginning of line. And then mixing(Promoting the moisture to 40%-45%), granulating, drying, cooling, screening, packing.

After screening, the finished size organic fertilizer granules into packing hopper for packing.The big granules will be crushed into powder,and then together with the fine powder after screening, back to mixing for re-granulating.
Organic fertilizer Fermentation Equipment Turner machine can prevent compost temperature too high.You can add water or strain when ferment,it also can mixing material when turning. This type is
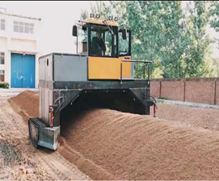 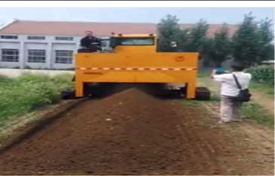 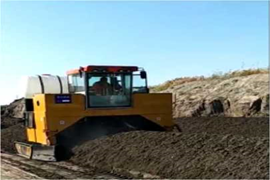
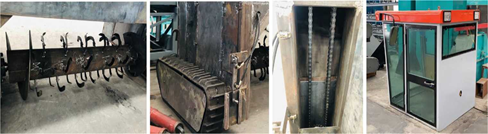
Crawler type turner machine.
Fermentation Cost | Picture | Description | Model | Quantity | EXW Price |
|
| 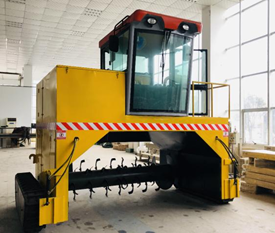 | Crawler turner machine 1.Width of pile:3000mm 2.Height of pile:900-1200mm 3.R6105-110KW/140hp 4 .Maximum Rotational Speed: 2200 revs per min. 5 .Rated Horsepower Speed: 2200 revs per min. 6 .Working Speed: 10-50 m/min. 7 .Three forward gears, A reverse 8 .Production capacity: 1000-1800m? per hour 9.Overall Dimensions:4.3*2.65*3.15M This machine need one 40ft high container for shipping. Advantages: Don/t need build fermentation tanks. | 3000 | 1 set |
| 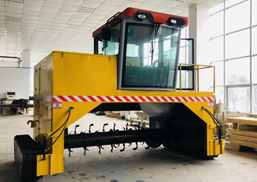
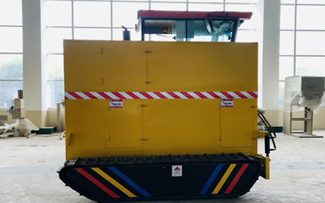
| 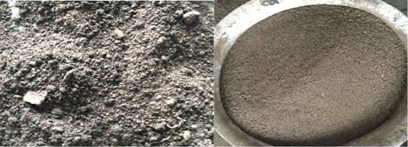 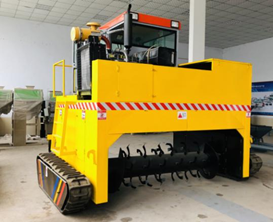
|
|
Organic Fertilizer Crushing & Granulating Area Production Technology Flat Drawing (just for reference):
1 . Fermentation machine 2 . Loader Hopper 3 . 9M Belt Conveyor machine 4 .110 Crusher machine 5 .10M Belt Conveyor machine 6 .1.8*6M Screen Machine 7 .8M Belt Conveyor Machine 8 . 8M Belt Conveyor Machine 9 .12M Belt Conveyor for return 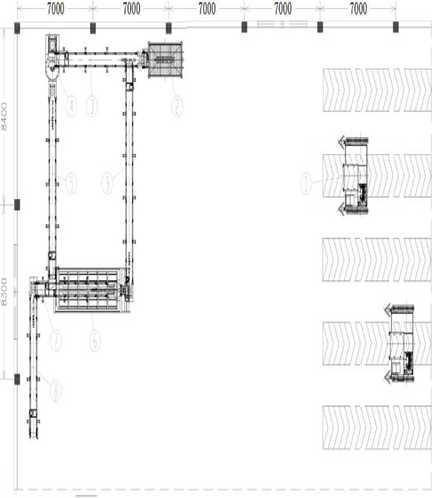
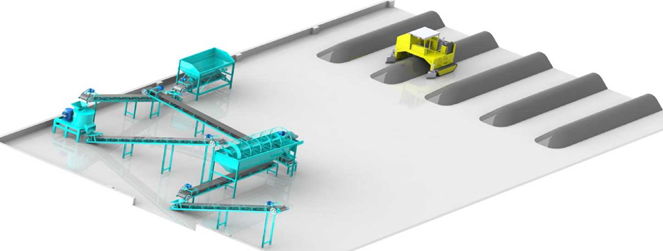
Batching machine 12M Belt Conveyor Machine 18M Belt Conveyor Machine Double shaft mixer machine 5.8M Belt Conveyor machine 1.01.5 granulator machine 7.16M Belt conveyor machine 8.1.818M dryer machine 11M Belt Conveyor machine 10.5M Belt Conveyor machine 1.5*15M Cooler Machine 12M Belt Conveyor Machine 1.8*6M Screen Machine 14M Belt Conveyor Machine 15.16 screw feeding machine 16.coating oil melt pot 1.5*6M Coating Machine 12M Belt Conveyor machine Finish Production Hopper Packing machine Chain Crusher machine 7M Belt Conveyor for return 23.7M Belt Conveyor for Return Hot Air Stove Dust collect room for dryer Air Fan for dryer Dust collect room for cooler Air fan for cooler Water pot and chimney
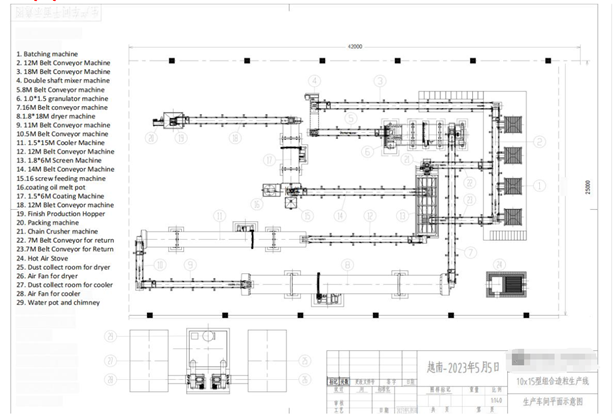
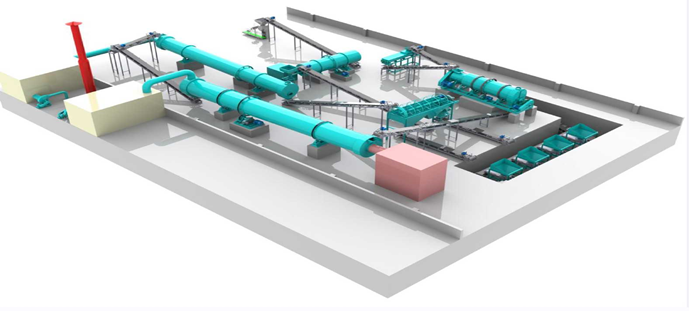
The fertilizer granules of Organic fertilizer rotary drum granulation production line:
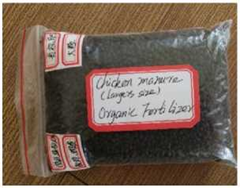 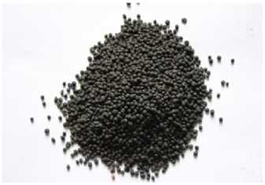 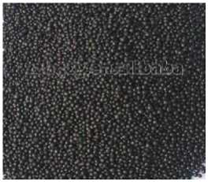 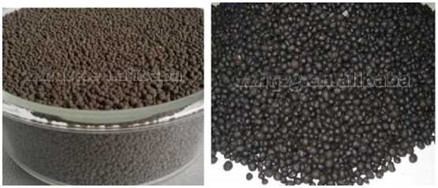
8-10 tons/hour Organic Fertilizer Granulation Production Line Machines List Crushing Screening Area: |
| NO. | Commodity | Picture | Model | Power (Kw) | Specification | QTY (Set) | EXW Price (USD/Set) |
| 1 | Loader Feeding Hopper | 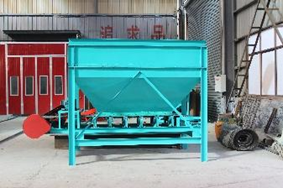
| 2000*3000 | 3kw+4kw | 1.Function: feeding the materials with loader; 2.Capacity: 8-10tons/hr 3.Material Spec: Q235 carbon steel; 4.Structure Characteristics: with belt conveyor and broken device; 5.Weight: 860kgs 6.Size: 4.16*2.1*3m | 1 |
|
| 2 | Vertical Semi-wet Material Crusher | 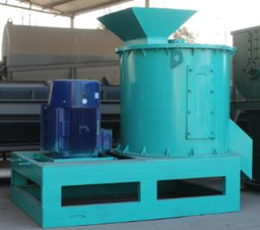
| 110 | 45kw | 1.Function: crushing the compost materials into fine powder; 2.Capacity: 8-10tons/hr 3.Material Spec: Q235 carbon steel; 4.Structure Characteristics: with long and short blades; 5. Size: 2.25*1.24*1.8m | 1 |
|
| 3 | Rotary Screening Machine | 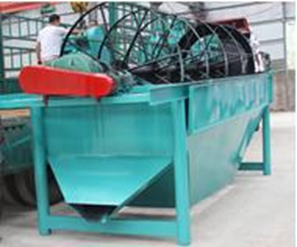
| GS1.8*6 | 7.5kw | 1.Function: small stones, plastics, glass slag and other impurity are separated from the fine powder; 2.Capacity: 8-10tons/hr 3.Material Spec: Q235 carbon steel; 4.Structure Characteristics: with rubber beating device(to prevent blocking) and stainless steel screen; 5.Weight: 2.6tons 6. Size: 7.7*2.1*2.9m | 1 |
|
| 4 | Belt Conveyor | 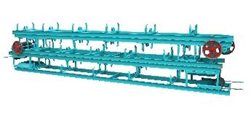
| B500 (total length: 47m) | L:8m*2 3kw*2 L:9m 3kw L:10m 3kw L:12m 4kw | 1.Function: conveying the materials; 2.Capacity: 5-10tons/hr 3.Material Spec: national standard 100mm channel carbon steel; 4.Rubber belt width: 500mm; 5.V-belt driving type, with safety cover; | 5 |
|
|
|
| Granulating area |
|
|
| NO. | Commodity | Picture | Model | Power (Kw) | Specification | QTY (Set) | EXW Price (USD/Set) | 1 | 4 Hoppers Automatic Batching Weighing Belt Conveyors | 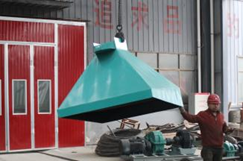 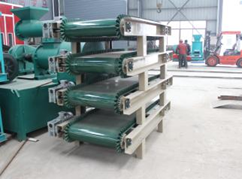 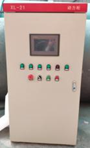  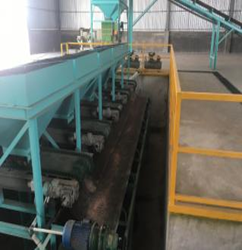
| BP-500 | 1.1Kw*5 | 1 .Function:Practicing automatic continuous batching process according to customer's formula. Dosing Error: +0.5%. 2 .Machines Composition: 2.1, 5 sets of feeding hoppers 2.1.1, Hopper size: 1.5*1.5m, Volume:1.5m CBM. 2.1.2, Hopper material: 3mm thickness Q235 carbon steel. 2.2, 5 sets of weighing belt conveyors 2.2.1, Each weighing belt conveyor with 1 pic of rotary encoder and 1 pic of weighing sensor(weighing range:100Kgs) 2.2.2, Weighing conveyor length:2.0m Weighing conveyor width:0.5m, Weighing Conveyor Power: 1.1kw/set. 2.3,1 set of HMI general control cabinet 2.3.1, Electrical device: Schneider Electric Device 3.Operation Instruction: 3.1,1 labor feed 1 hopper, totally need 4-5 labors. 3.2, The batching process is finished automatically. 4,Feeding capacity: 5-30 t/h | 4 sets |
| 4 | Double Shafts Mixer | 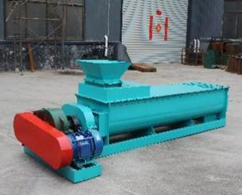
| ZYQ-QZ500 | 22kw | 1.Function: make the different solid material and liquid mixing evenly; 2.Capacity: 10-15tons/hr 3.Material Spec: Q235 carbon steel; 4.Structure Characteristics: with double shafts paddle; 5.Weight: 2.98tons 6.Size: 4.5*1.6*1.27m | 1 |
|
|
|
| 5 | Uniform Feeder | 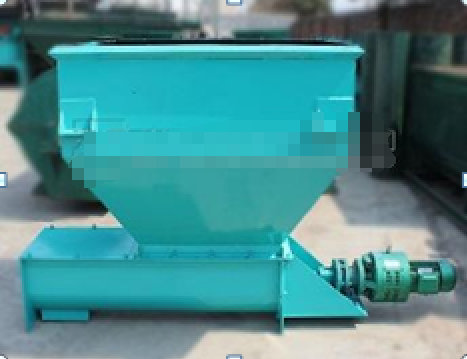
| 1.5m*1.5m | 3kw | 1.Function: store materials to make them evenly feed; 2.Capacity: 8-10tons/hr 3.Material Spec: Q235 carbon steel; 4.Structure Characteristics: with screw conveyor; 5.Weight: 360kgs 6.Size: 1.8*1.6*1.6m | 1 |
|
| 6 | New Combined Type Organic Fertilizer Granulator | 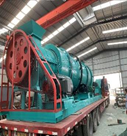
| YSL2-1000/1 500 | 75kw+11kw+1 8.5kw | 1 . Function: it is a new type of combined granulator suitable for big capacity. It combines the stirring granulation and rotary drum granulation, with former stirring and latter rotating drum; 2 .Capacity: 8-10tons/hr 3 .Material Spec: Q235 carbon steel; 4 . Structure Characteristics: with many stirring inside; 5 .Weight: 7.8tons 6.Size: 5.95*2.15*2.35m | 1 |
|
| 7 | Rotary Dryer | 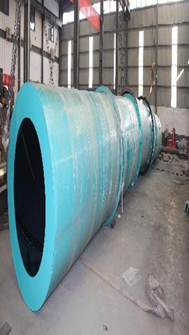
| HG18180 | 18.5kw | 1.Function: reduce the moisture ofthe granules; 2.Capacity: 8-10tons/hr; 3.Material Spec: Q235 carbon steel; 4. Structure Characteristics: with 1 set of seal head; 1 set of seal tail; 1 set of drying body with gear rolling and rolls;2 set of roll bearing base;1 set of driving base;1 pic of hot air pipe; and 2 pics of straight air pipe; and 1 pics of elbow; 5.Diameter: 1.8m;Length:18m;Steel thickness:14mm 6.Weight: 16tons 7.Size: 18*2.15*2.15m Remark: the rotary dryer is with the temperature couples and temperature display system. | 1 |
|
| 8 | Rotary Dryer Hot Air Fan | 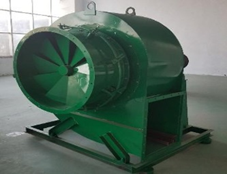
| 8C | 22kw | 1 .Function: Inducing the hot air from the hot air stove, and through the dryer machine body, pass the hot air fan, and through the dust collecting room, and end from the chimney. 2 .Air flow:17463-32380m3/hr Air Pressure:2478-1816Pa 3 .The hot air fan cost is included by the rotary dryer machine; | 1 | / |
| 9 | Rotary Cooler | 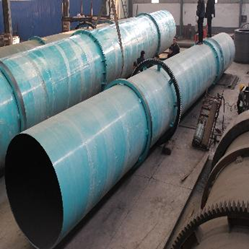 | LQ15150 | 15kw | 1 .Function: cooling the fertilizer granules to normal temperature; 2 .Capacity: 8-10tons/hr 3 .Material Spec: Q235 carbon steel; 4 .Structure Characteristics: with 1 set of head; 1 set of drying body with gear rolling and rolls; 2 set of roll bearing base;1 set of driving base;1 pic of straight pipes; and 1 pics of elbow; 5.Diameter: 1.5m;Length:15m;Steel thickness:12mm 6.Weight: 9.2tons 7.Size: 15.6*1.85*1.85m | 1 | 10 | Rotary Cooler Air Fan | 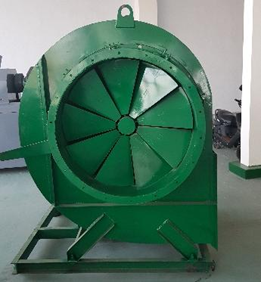
| 6c | 18.5kw | 1 .Function: Inducing the normal natural air, through the cooler machine body, pass the cooler air fan, and through the dust collecting room, and end from the chimney. 2 .Air flow:10314-20628m3/hr Air Pressure:2734-1788Pa 3 .The cooler air fan cost is included by the rotary dryer machine; | 1 | 11 | Rotary Screening Machine | 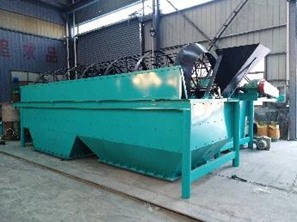
| GS1.8*6 | 7.5kw | 1 .Function: screening the different size granules to get final products; 2 .Capacity: 8-10tons/hr 3 .Material Spec: Q235 carbon steel; 4 . Structure Characteristics: with rubber beating device(to prevent blocking) and stainless steel screen ; 5 .Weight: 2.6tons 6 .Size: 7.7*2.1*2.9m | 1 |
|
| 12 | Coating Machine | 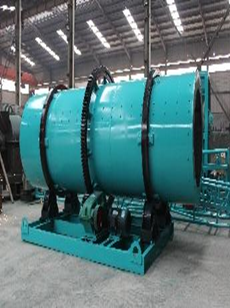
| BM1.5*6.0 | 5.5kw | 1.Function: coating the bio bacteria or anti-caking agent; 2.Capacity: 8-10tons/hr 3.Material Spec: Q235 carbon steel; 4.Structure Characteristics: with 1 pc of gear roll and 1 rolls;1 set of driving bearing cast base, 2 sets of roll bearing cast base; 5.Diameter: 1.5m; Length:6.0m;Steel thickness:12mm. 6.Weight: 4.45tons 7.Size: 6.0*1.9*1.9m | 1 |
|
| 13 | Powder Coating Screw Feeder | 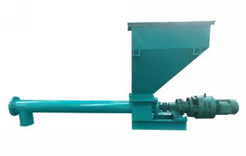
| 0130 | 1.1 kw | 1. Function:quantitive feeding the coating powder agent. 2. Separated adjustable speed control cabinet. 3. Electromagnetic governor speed controlling. 4. With 0130mm screw conveyor,1.0m3 storage hopper. 5. Separated control panel. 6. Size:2.25x0.63x0.8m. 7. Weight:200kgs. | 1 |
|
| 14 | Liquid Coating Electric Heating Melt Pot |
|
| 1.0m3 (Total 32.25 Kw) | 1.5Kw + 30kw + 0.75kw | 1. Function:Meting the solid paraffin into the liquid, the spraying the paraffin liquid on the surface of NPK fertilizer granules, and make the fertilizer slow release. 2. With galvanized liquid pipes,heating device, metering pump, and nozzles. 3.SS304 melt pot with 1.0CBM volume. 4 . Separated control panel. 5 .Meting heating power:30kw, Pump motor:1.5kw, Blending device motor:0.75kw. | 1 | 8056.50 |
| 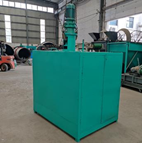 |
|
|
| 13 | Finished Hopper | 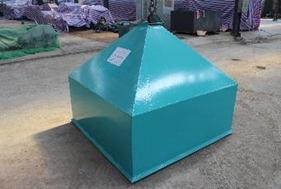
| 1.5*1.5 | / | 1.Function: store the finished fertilizer granules for packing machine; 2.Capacity: 1.2m3 3.Material Spec: Q235 carbon steel; | 1 | 733.6 | 14 | Packing Machine | 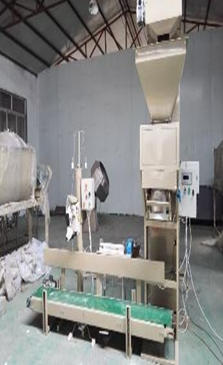
| DCS-25 | 0.55kw+0.37k w | 1.Packing machine parts: (1) Packing machine body (2) Sewing Part (3) Belt Conveyors (4) Air Compressor 2.Packing range: 25-50kgs/bags 3.Packing bags size: >= Diameter: 300mm 4.Granules packing speed: 8-10 bags/ Min( In theory), 4-6 bags/Min( In practice) 5.Motor: (1) Sewing motor 0.37kw (2) Belt conveyor motor 0.55kw (3) Air compressor motor 2.2kw 6.Packing Machine Panel Electric: 220-240v, 1 phase, 50hz | 1 | 7008.5 |
| Air Compressor | 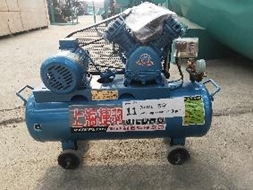
| / | 2.2kw | Function: provide are pressure for the air pump on the packing machine; | 1 |
|
| 15 | Chain Crusher | 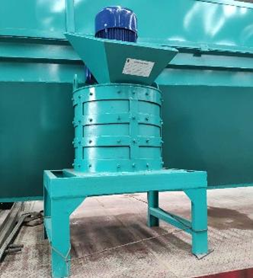
| LP800 | 15kw | 1 .Function: crushing the big granules from the third output of rotary screening machine into power shape for re-granulating; 2 .Capacity: 2-8tons/hr 3 .Material Spec: Q235 carbon steel; 4 .Structure Characteristics: with chains crushing blades inside; 5.Weight: 500kgs 6.Size: 1.46*1.18*1.7m | 1 | 2489.00 |
| 16 | Belt Conveyor | 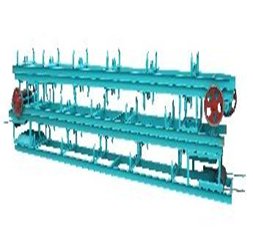
| B500 (total length: 122m) | L:5m 3kw L=7m*2; 3kw*2 L=8m;3kw L=11m;4kw | 1.Function: conveying the materials; 2.Capacity: 5-10tons/hr 3.Material Spec: national standard 100mm channel carbon steel; 4.Rubber belt width: 800mm; 5.V-belt driving type, with safety cover; | 11 | 21575.70 |
|
| L=12m*3; 4kw*3 L=14m;4kw L=16m;4kw L=18m;5.5kw |
| 17 | Chimney | 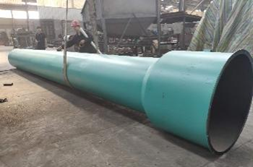
| Ø1000 | / | 1.Function: smoke exhaust; 2.Height:9m 3.Blow ground level: ø1100mm; Above ground level: ø1000mm; | 1 | 3602.5 |
| 18 | Electric Control Box | 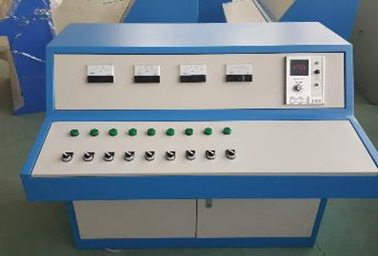 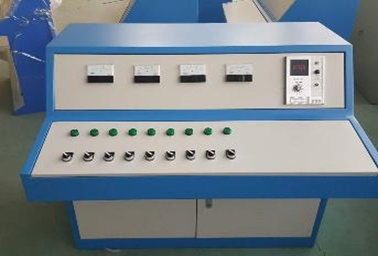
| EC-22 | / | Function: control all the power motors of the whole production line with Siemens PLC control system; | 2 | 10545.50 |
| 19 | Hot Air Stove & Dust Chamber | 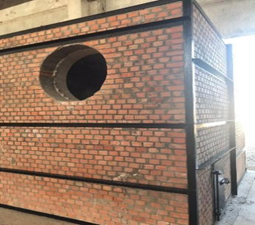
| / | / | If the buyer want to build them, we will provide all the construction drawings and technical. | / | / |
| Total Granulation line |
|
| 315.97kw |
| 33Sets |
|
|
Remark: After confirming the order, our company will provide the following detailed foundation building drawings within 10 days: 1. The whole production line layout drawing; 2. The construction drawing of pits for the batching machines; 3. Position confirmation drawing; 4. The foundation base construction drawing of granulator; 5. The foundation base construction drawing of 1.8*18m dryer; 6. The foundation base construction drawing of 1.5*15m cooler; 7. For the cyclone dust collector and chimney, you can buy them from our factory, if you want to build the dust chamber and chimney by yourself, we can provide the detailed construction drawings for you; 8. The cable groove and position in workshop drawings of the whole production line; 9. The details foundation base construction drawing of all the machines�?bracket. All the need to build by buyer under the guiding of the seller, we provide the detailed civil drawings after the first payment. The quotation is only the price of all the machines, excluding the installation accessories, such as the stand of the belt conveyor and ladders, etc. (please don’t worry, it’s just a small cost). Warranty: 1 year for the whole line, Except for the wearing parts. After-sale service: 1 .We will arrange an engineer to buyer’s company for installation guide, training workers, the buyer should bear our engineer’s round-trip air cost and accommodation on buyer ‘s company. 2.Before the installation, the workshop should be ok for installation ,and during the installation, the buyer provide all the labors and engineering plant. If because of the reason above, leading to the delay on the installation time. The buyer should bear the cost. 3.Engineer available overseas service installation guide and training workers(Client pay for costs of round-trip air tickets, food and accommodation and labor's salary, salary is 200 -350 per day, need about 20-30 days). Could offer all the instructions of machines for installation.
Crushing Area and Granulating Area:
Before Crushing and Screening After Crushing and Screening 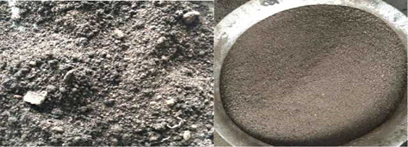 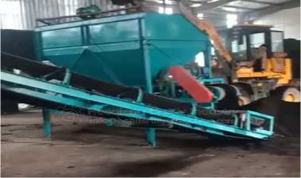
The Granules Sample of Organic Fertilizer 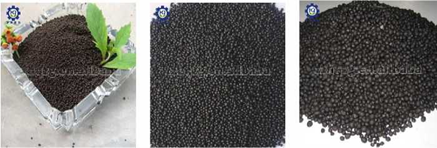 
1.Loader Feeding Hopper • The machine is mainly used for loader feeding. The machine with breaker and belt conveyor, the breaker can crush materials and prevent blockage when discharge.
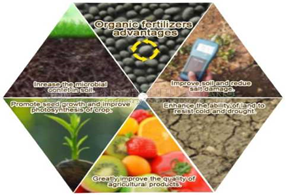
2.Semi-wet Material Crusher • After fermentation (composting), crushing the compost materials into fine powder to granulate. The Granules Sample of Organic Fertilizer Advantage: it can crush high moisture of materials, widely used in crushing organic fertilizer materials. The vertical type can prevent the material from sticking or blocking when the moisture is high
3.Double Shafts Mixer • Mixing the different materials or water evenly. • Water or trace elements can be added here. 4.Screening Machine • Screening machine is used to screen fine powder and waste. •The screening machine with two outlets, one is screen out the fine powder, the other is screen out the waste (like small brick, stone, glass, plastic and so on). 5.Combined Type Organic Fertilizer Granulator • After being crushed and mixed, the fermented materials are enter the new type organic fertilizer granulator for granulating. •There are many stirring teeth inside of this granulator, which can make round shape granules .
The Advantage of Organic Fertilizer The 3D Drawing of The Crushing Machines
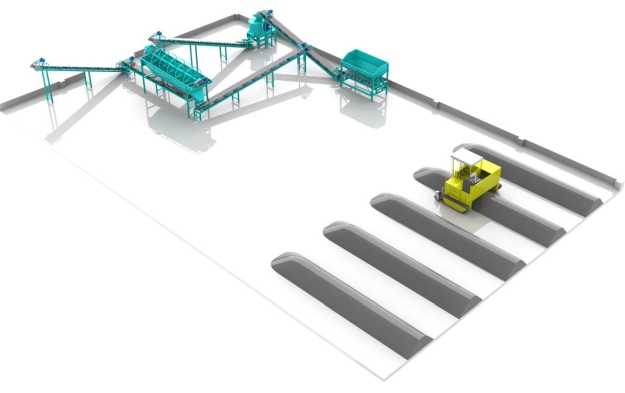
6.RotaryDryer • The rotary dryer is used to reduce the moisture of the granules, and it has the function of secondary granulation. The dryer through an induced draft fan to draw hot air from the combustion chamber to dry granules.
8.Rotary Cooler • The rotary cooler is used to reduce the temperature of the granules for packing, hot granules are easy to stick together and with moisture, so need to use the cooler to cooling before package. •The cooler uses the induced draft fan to draw the outside wind to cool the granules at the same temperature as the outside.
The 3D Drawing ofThe Machines
machine. 9.Rotary Cooler Air Fan • The induced draft fan can make the hot air in the cooler exchange and convection with the airflow in the air quickly. • The performance of the fan is closely related to the cooling effect of the cooler. 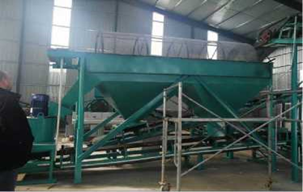
10.Screening Machine • Screening machine is used to screen small granules, final product granules and big granules. 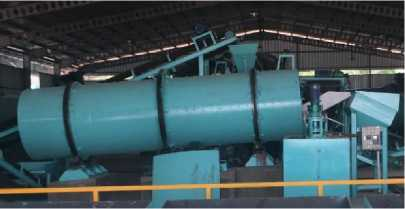
•The small granules screened out will be granulated twice after entering the mixer, and the big granules will be granulated again after crushing, and the final product granules will be packed in the packing
11.Coating Machine • The machine is mainly used to coating the bio bacteria or anti-caking agent. In the design ofthe drawing, you can choose to use the coating machine sometimes or not, which will not affect the layout of the other machines.
12.Finished Hopper • Finished product hopper for packing machine. • Used for storing and feeding granules into packing machine. 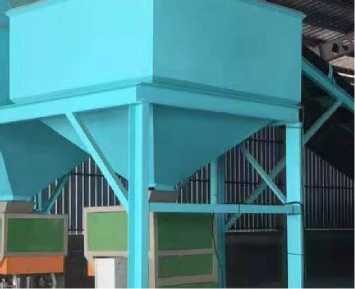
13.Packing Machine • The packing machine include the filling bags part, weighing part, electric control box with control panel, sewing machine or hot melting machine, belt conveyor and air compressor.
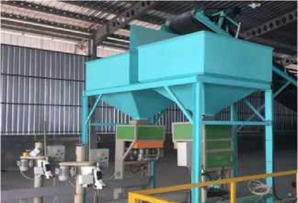
14.Chain Crusher The big granules screened out by the screening machine are crushed and put into the granulator for secondary granulation. 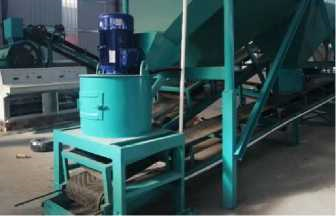
The 3D Model of Organic Fertilizer Granulation Production Line
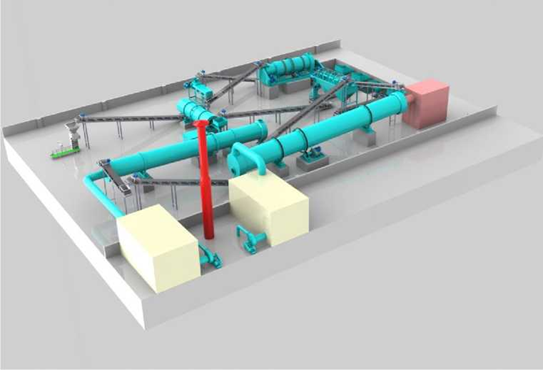
15.Belt Conveyor • It is used for material transportation between machines.

16.Hot Air Stove • Burner can convert heavy oil, natural gas, LPG or other fuel into flame. •The hot air stove contains refractory materials to avoid direct contact between flame and granules. 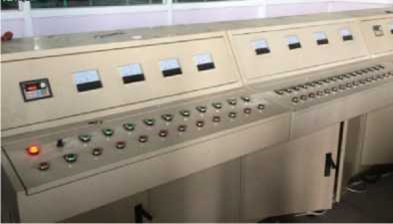
17.Electric Control Box • Control the motors of all machines in the whole production line, which can be started by one key. •There are indicator lights, emergency stop button, start and stop buttons for motors on all machines, etc.
|