Product | Output | Purity | Pressure MPa | Temperature �?/span> | Oxygen | 50Nm³/h | �?/span>99.6% | 15 | Normal |
ASU KDO-50�?/span>Ready Installed�?/span> Quote No: | 何工25202404190164-93908 |
Price List | No. | Item Name | Model or Spec. | Qty. |
| Remark | 1 | Air Compressorer | G90 | 1 |
| Atlas Copco | 2 | Air precooling unit | GAYL-1200/10 | 1 |
| Jialian | 3 | Air purification | HXK-1200/10 | 1 |
| Nuzhuo | 4 | Column | FO-50 | 1 |
| Nuzhuo | 5 | Expander | PLPK-26.67/0.3-0.025 | 2 |
| Hangyang | 6 | Instrument Control System | PLC | 1 |
| Zheda Central Control | 7 | Electric Control System |
| 1 |
| Siemens | 8 | Cryogenic Liquid Pump | SBP100-150/150 | 1 |
| Sanjin | 9 | Inflatable row | 1*6 | 2 |
| Nuzhuo | Containerized Ready Made System Cost(Non-installation type) |
|
|
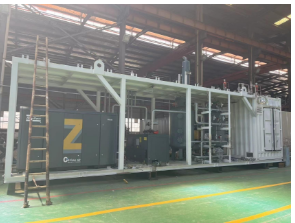
Cryogenic ASU Technical Scheme Specification: 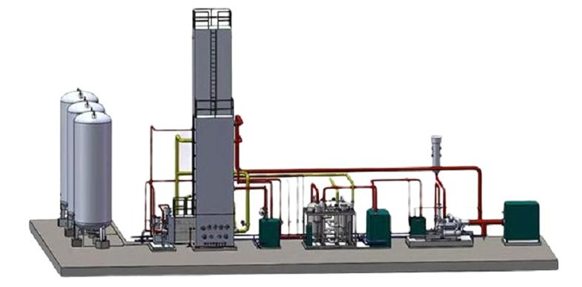
1. Company Profile Our locating by the Fuchun River of Hangzhou, is known as the professional manufacturer of air separation industry. The factory owns 14,000 m² total plant area. There are all together 106 employees, including over 50 workshop workers and 5 senior technicians. The office building, mainly for sales and marketing department, is in Fuyang, about 25-mins driving away from the factory. It is in a modern office building, and we one of the whole floor which occupies 2000 m². devotes to provide the best solutions for customers with various demands of the air separation products, especially Oxygen and Nitrogen. Our product series overwhelmingly cover the whole air separation industry, such as large-scale cryogenic air separation series; pressure swing adsorption Series, purification equipment series; air compression & purification drying machine; low temperature storage tank etc. We also have advanced production lines for intelligent control valve. The company have abundant overseas project experiences for all kinds of air separation products solutions in various industries. For examples, Cryogenic Air Separation Plant in Russia; Liquid Oxygen Storage tank&Gas station in Turkey; PSA Nitrogen Generator in Thailand; Oil Free Compressor in South Africa and Container Oxygen Generator in Chile. As long as you have needs for Oxygen, Nitrogen, liquid oxygen or liquid nitrogen, or other air separation plant related components such as compressed air purification system, compressed air filter, we are here to provide you with proper solution in professional ways.
2. Project Overview According to the friendly negotiation between the two parties, the scope of responsibilities is divided as follows: 1.1. The seller undertakes the scope of responsibility within the boundary of the air separation plant: (1) Process design, instrument electrical design, equipment design, and engineering design of the air separation plant. (2) The scope of supply of process equipment is as follows: 1 screw compressors, 1 air pre-cooling unit, 1 molecular sieve purification system (including molecular sieve and alumina), 1 fractionation tower system (including pearlescent sand), 2 sets Complete supply of expander system, 1 oxygen booster, 1 sets of filling platoons and instrument control system, electrical system, spare parts and special tools used in supporting the above process equipment; see "Appendix 5 Process Equipment and Instrument Electricity" for details Scope of supply". (3) The installation materials supplied by the seller within the boundary of the air separation plant include: process piping, cryogenic liquid piping from cold box to cryogenic storage tank, steel structure pipe gallery and supports, steel structure equipment and valve maintenance platform, Cable tray, power cable, instrument cable, instrument root valve, instrument sampling pipe (stainless steel), anti-corrosion and thermal insulation materials, cutting gas, solder and other auxiliary materials required for installation work. (4) The installation work in the boundary area of the air separation plant includes the following: the installation of the equipment mentioned in serial number (3), the installation of ancillary instruments and electrical appliances, the installation of process pipes, steel structure pipe gallery and brackets, steel structure equipment and valve maintenance platform Installation, installation of power cables and instrument cables, installation of cable trays, anti-corrosion and heat preservation work, filling work of molecular sieve purification system packing, filling work of pearl sand, the insulation material in the cold box, linkage test work, official start-up work, flaw detection, Also includes the installation tools required for the above installation work. (5) Junction point: the junction point of high and low voltage cables is bounded by the inlet end of the high and low voltage cabinet of the seller; the circulating water is connected by the buyer to 1 meter outside the boundary of the air separation unit; the junction point of the product liquid is at the liquid nitrogen storage tank; nitrogen gas It is the interface of the buffer tank before the out-of-bounds area; (6) Performance assessment, document delivery, technical service and after-sales service related to the air separation plant. (7) Assist the buyer to complete other work related to the air separation plant. 1.2. The buyer undertakes the scope of responsibility within the boundaries of the air separation plant: (1) Responsible for the preliminary survey and detailed survey of the land within the boundary of the air separation plant, as well as the three connections and one leveling work within the boundary. (2) Responsible for the civil works in the boundary area of the air separation plant (mainly greening work, central control room, power distribution room, pipe trench and cable trench), compressor workshop and Driving in the pump room, electrical professional lightning protection and anti-static, factory lighting, equipment lighting and telecommunications, structure, water supply and drainage, inspection and testing, security monitoring, HVAC, fire engineering design, materials, and construction. (3) Water, electricity, pressure test gas and mechanical materials for the commissioning and start-up of the air separation plant. The production process of this air separation unit is a domestic advanced process, and the main equipment is imported or domestic advanced. The device has many advantages such as high safety, reliable operation, strong operability and low energy consumption. 3. Basic conditions of device design (subject to the parameters provided by the buyer) 3.1 Atmospheric conditions design point |
| Atmospheric pressure | KPa�?/span>A�?/span> | Environment Temperature | 30�?/span> | Relative humidity | 70% | Oxygen content of Hb | 20.95% O2 | 3.2 Atmospheric temperature |
| Maximum temperature | 35�?/span> | Minimum temperature | -25�?/span> | 3.3 Seismic intensity | 6 degree | 3.4 Raw material air miscellaneous conditions |
| CO2 | �?50ppm | C2H2 | �?.5ppm | H2 | <0.7ppm | CO | �?.5ppm | N2O | <0.3ppm | SOX | <0.2ppm | CnHm (regardless of C2H2) | �?ppm | Dustiness | 30mg/m³ | 3.5 Utility project condition�?/span> |
| 3.5.1 Cycling water |
| Inlet temperature | 33�?/span> | Temperature rise | 10�?/span> | Inlet pressure | 0.5 Mpa (G) | Pressure of return water | 0.25 Mpa (G) | Dirtiness resistance | 3.4*10-4 m³·K/M | 3.5.2 Power supply�?/span> |
| Standard power supply | 380V�?/span>220V | Frequency | 50+0.5/-0.5 Hz | 3.5.3 Instrument air (supplied by equipment after start-up) | Pressure | 0.5MPa | Temperature | 32�?/span> | Dew point | -40�?/span> | Flow | 100Nm³/h |
4. Main technical parameters of the device 4.1 Output and purity 4.1.1 Main production A Product | Output | Purity | Pressure MPa | Temperature �?/span> | Oxygen | 50Nm³/h | �?/span>99.6% | 15 | Normal |
5. Utilities consumption 5.1. The following process air (including instrument air) is required for the air separation unit of the raw material air to produce the above products Raw material of air gas flow�?/span> 600Nm3/h Air pressure�?/span> 1.0 MPa(G) 5.2 Main Consumption No. | Device Name | 380V | Water Consumption | Qty | Remark | shaft/motor power KW/set | t/h | Set | 1 | Air Compressor | 80/90 |
| 1 |
| 2 | Air Precooling Unit | 10/13 | 6 | 1 |
| 3 | Electric heater | 11/30 |
| 1 | 4h auto switch | 4 | Instrument control system | 3/3 |
| 1 |
| 5 | Cryogenic Liquid Pump | 8/8 |
| 1 |
| Total shaft power | 112 | 6 |
|
|
6.Brief description and characteristics of the process 6.1 Brief description of the process After the air is removed from the dust and other mechanical impurities by the suction filter, it enters the air compressor and is compressed to 1.0MPa (G), and at the same time, it is cooled to �?/span> 40 ° C in the terminal cooler, and then cooled to 8 ° C by the refrigeration unit, and then enters the water separation unit. The water in it is separated by the device, and then enters the molecular sieve adsorber to remove H2O, C2H2 and CO2 in the air to obtain purification. There are two molecular sieve adsorbers, which work alternately, that is, when one is adsorbing, the other is regenerating. Factory air and instrument air are extracted after molecular sieve. The purified air is divided into two paths: one path enters the fractionation tower, and enters the bottom of the rectification tower after being cooled in the main heat exchanger; the other path enters the fractionation tower, which is cooled in the main heat exchanger and then enters the expander for expansion and then enters the upper tower. The middle part participates in the upper column rectification to provide cooling capacity for the system. The rising gas in the lower column is increased in nitrogen content by contact with the reflux liquid. The required reflux liquid nitrogen comes from a condensing evaporator at the top of the lower column, where oxygen is evaporated and nitrogen is condensed. •Sewage nitrogen loop: A stream of dirty nitrogen is used for the regeneration of the molecular sieve adsorber, and a small part enters the cold box to inflate the cold box. • Dry air for thawing: The air separation equipment instrument and the dry air for thawing (in normal working state) are extracted from the outlet of the molecular sieve adsorber and sent to the instrument air network. •Instrument air: self-use instrument air self-sufficiency Liquid discharge: into the liquid storage tank •Exhaust: The exhaust of the equipment is first sent to each muffler and then discharged into the atmosphere. 6.2 Process flow characteristics 6.2.1 Air Compression System �?/span> Adopt imported screw air compressor, high efficiency, low consumption, stable and reliable operation. 6.2.2 Air pre-cooling system �?/span> The air-conditioning unit adopts the combination of imported screw refrigeration compressor and all imported refrigeration components, load tracking of slide valve + hot gas bypass fine-tuning to stabilize the cooling air temperature, stainless steel tube and shell heat exchanger and collision + heavy sedimentation water separator combination automatically Separation of condensed water, air resistance loss �?/span> 10kPa. Simple and convenient operation, noise �?/span> 70dB (A). �?/span> A water separator is set to remove free water, and a manual and imported automatic drain is set at the lower part to remove accumulated water regularly. 6.2.3 Purification system �?/span> The purifier adopts a vertical single-layer bed, which shows the advantages of 13X-APG and the resistance loss is small. The built-in filter can be used for both blowing and purifier regeneration. High-efficiency electric heaters ensure thorough regeneration of molecular sieves. �?/span> The switching cycle of the molecular sieve adsorber is 8 hours, the number of regenerations is small, and the power consumption is low. �?/span> The switching valve adopts Nuzhuo products, with reliable action, zero leakage, grade VI seal, and long service life. �?/span> The pressure equalizing valve adopts the regulating ball valve and cooperates with the pressure switch to realize the switching without impact. �?/span> The electric heating tube adopts stainless steel straight rod type, which is easy to disassemble. When the electric heating tube fails, it can be extracted by a single piece, which is convenient for replacement. The electric heaters are configured according to one use and one backup. �?/span> The power of the electric heater is controlled in three groups. When the outlet temperature of the heater is lower or higher than the set parameter, the power combination will automatically stop or start. �?/span> The purifier regeneration heating gas volume and the electric heater are equipped with an interlocking device, the gas volume is lower than the set value and the circuit breaker is automatically protected, and when the gas volume is higher than the set value, it is automatically restored. 6.2.4 Fractionator system �?/span> This device does not have a separate heating system, and the fractionation tower is heated, cooled, liquid-accumulated and purified in one go, and the operation is simple and quick. �?/span> Adopt aluminum plate-fin heat exchanger and aluminum convection sieve plate tower. The whole fractionation tower equipment pipeline adopts argon arc welding, which is safe and reliable, and realizes the continuous and stable operation of the device load at 75-105%. �?/span> The turboexpander adopts gas bearing, which is simple and reliable, easy to operate and has high isentropic efficiency. The expander cold box is set separately for easy maintenance. �?/span> The tower body and main pipeline in the cold box are made of high-strength aluminum alloy material or stainless steel material to increase the strength and reduce the torsional damage of the pipeline. �?/span> The equipment brackets, pipes and valve brackets in the cold box should be made of stainless steel or aluminum alloy. �?/span> The cold box is insulated with pearl sand and slag wool to ensure the minimum cooling loss. �?/span> The instrument pipelines in the cold box should be arranged centrally, adopt protective measures, and be beautiful. �?/span> The structure of the cold box needs to ensure the overall strength and the requirements of anti-vibration and wind resistance, to ensure the load-bearing capacity of the cold box, and to have a beautiful appearance. �?/span> When the cold box is running, it is equipped with sealing gas protection and safety devices. Equipped with a sufficient number of manholes and pearl sand loading and unloading ports, allowing personnel at certain positions to easily enter the cold box for maintenance operations and the filling and disassembly of cold insulation materials. �?/span> The main equipment in the cold box is set to electrostatic grounding. �?/span> The connection between the cooling valve in the cold box and the pipeline is all welded, Nuzhuo products. The low temperature manual valve adopts Hangzhou Nuzhuo products.
7. Scope of supply of unit equipment (including but not limited to the following, which are complementary to the PID diagram) 1. The scope of supply provided by the seller is based on the principle of overall supply of each system and single unit. The scope of supply of each system and each unit, except for the main equipment and single unit, also includes necessary pipe fittings, paired flanges, anchor bolts, etc. in the boundary area. 2. Various valves for each system and each unit are supplied in complete sets. 3. Process pipelines, valves, instruments, fittings, etc. between systems. 4. The design of this equipment is based on the basic design conditions of the user's site, and the various equipment data provided are for reference only. To be determined at the final design stage, if the seller's final design changes, the commercial price will be adjusted accordingly. 7.1 Air compressor unit (technical parameters are subject to the final design) (1) Manufactured by Wuxi Atlas factory, designed and produced according to international standards for Atlas series screw air compressors, with high compression efficiency, good reliability and low energy consumption; it will leave the factory after testing in the production factory; (2) The impeller of each stage runs at its optimum speed, and the ternary flow design has high stage efficiency; (3) The high-efficiency intercooler with pull-out type and fins is adopted, and the inter-stage cooling effect is good; (4) Constant pressure control, PLC + LCD touch screen data display, adjust the gas volume within the maximum possible range, with anti-surge operation, automatic pressure control, impeller vibration alarm chain and other protection measures. Standard excuse, can be connected with the host computer; (5) Perfect oil circuit system to ensure the normal and safe operation of the unit; (6) The whole machine is skid-mounted, which is easy to install and saves infrastructure costs Manufacture�?/span> Atlas Copco (Wuxi) Compressor Co., Ltd. | 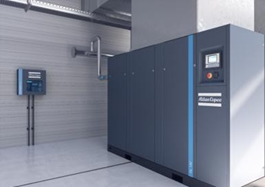
| Type�?/span>Screw Model�?/span>G90 | Place of origin�?Wuxi China | Parameter�?/span> | Medium | Air | Compression stage | Class 1 | Outlet air | 14.53Nm³/min | Inlet pressure/Temperature | 1.0Mpa(A)/35�?/span> | Outlet pressure/Temperature | 1.0Mpa(G)/�?5�?/span> | Connection diameter | DN50,PN16 | Shaft power | �?/span>80kw | Motor power | �?/span>90kw | Noise | �?5 dB(A) | Regulating range | 100% | Power | 3PH/380V/50HZ | Total Weight | 1450kg | Size(mm) | 1610x990x1870mm | Quantity | 1 sets |
8. Air pre-cooling unit 8.1 Device main description. 1. Using imported compressor, the refrigerant will never leak. 2. Using high-quality imported compressors and refrigeration components, the equipment can run continuously all year round and has a long service life. 3. Efficient gas-water separator and high-quality automatic drain valve ensure that the outlet air is free of liquid water. 4. Adopt advanced energy regulator to ensure that the compressor does not have to worry about frequent startup and shutdown. 5. The equipment displays the air inlet and outlet pressure, temperature, refrigerant high and low pressure, and the six main parameters are intuitive and clear. 6. The equipment has a remote signal interface for air inlet and outlet, a remote start and stop signal, and a fault signal for equipment operation, which is convenient for users to interlock and monitor. 7. The heat exchanger adopts (condenser, evaporator) with copper tube jacket as aluminum fin structure. The compressed air flows in the shell side, and the freon flows in the copper tube. This heat exchanger has a large heat exchange area, and heat exchange Good effect, good material, no corrosion, not easy to produce R410A leakage. Pre-cooling unit equipment parameters 8.2. Design conditions (provided by the buyer) 8.2.1 Design conditions of pre-cooling unit Cooling medium | air | Air input temperature | 42�?/span> | Air output temperature | 2-10�?/span> | Air flow | 600Nm3/h (0�?/span>,0.1013Mpa per hour) | Air input pressure | 1.0Mpa�?/span>G�?/span> | Thermal load | �?/span>224KW |
8.3. Equipment use conditions (public works) 8.3.1 Cooling water temperature: �?/span>32�?/span>; 8.3.2 Cooling water pressure: 0.2-0.4Mpa (G); 8.3.3 Power supply: 380V/220V AC three-phase four-wire system, 50Hz; 8.4. Pre-cooling unit equipment parameters Model | GAYL-600/10 | Cooling medium | Saturated moist air | Air inlet temperature | �?/span>42℃(Saturated moisture�?/span> | Air outlet temperature | 5-8�?/span> | Air flow | 600Nm3/h (0�?/span>,0.1013Mpa volume flow rate) | Air inlet pressure | 1.0Mpa�?/span>G�?/span> | Connecting diameter | DN100�?/span>HG20592B�?/span> | Thermal load | 33KW | Compressor type | 1 set of Scroll Refrigeration Compressor | Compressor Work Rate | 15HP | Input power | 10KW | Rated power | 13KW | Cooling capacity | 38KW | Cooling cycling water | 6T/h | Cooling water pipe diameter | DN40(screw joint) | Cooling type | Cycling water cooling | Water inlet temperature | �?/span>32�?/span> | Cooling water pressure | 0.2-0.45Mpa | Flange nominal pressure | 1.6Mpa | Working system | Work away | Process criterion | GB/T 10526 | Whole machine regulating range | 50%-100% | Cooling agent | R410A | Noise | �?/span>75dB | Power supply/Frequency | 380V/220V AC; 50Hz | Installation site | Smooth cement floor, no basic indoor installation | Control mode | PLC control |
8.5. List of main components of the pre-cooling unit No. | Item Name | Manufacturer | Qty | 1 | Scroll refrigeration compressor | Bitzer | 1 Set | 2 | Hot air bypass valve | Danfoss | 1 pc | 3 | Expanding valve | Danfoss | 1 pc | 4 | Filter dryer core | Danfoss | 1 pc | 5 | Suction filter | Jialian Customized | 1 pc | 6 | Refrigerant Windows | Danfoss | 1 pc | 7 | Dispensing head | Danfoss | 1 pc | 8 | Water extractor | Jialian Customized | 1 set | 9 | Solenoid valve auto drainer | Jialian Customized | 1 set | 10 | Low voltage electric components | Schneider | 1 set | 11 | Pressure meter | Jialian Customized | 4 pcs | 12 | Evaporator core | Jialian Customized | 1 pc | 13 | Evaporator barrel | Jialian Customized | 1 pc | 14 | Water condenser | Jialian Customized | 1 set | 15 | Ball valve | Danfoss | 1 pc | 16 | Control cabinet | Jialian Customized | 1 pc | 17 | PLC controller | Siemens or same class | 1 set | 18 | Frame, box board | Jialian Customized | 1 set |
8.6. Scope of supply of the supplier 8.6.1 Equipment body Item Name | Model | Qty | Precooling unit | GAYL-600/10 | 1 Set | Remark: With mating flanges, gaskets and fasteners, and anchor bolts. |
|